Amélioration continue : définition et outils
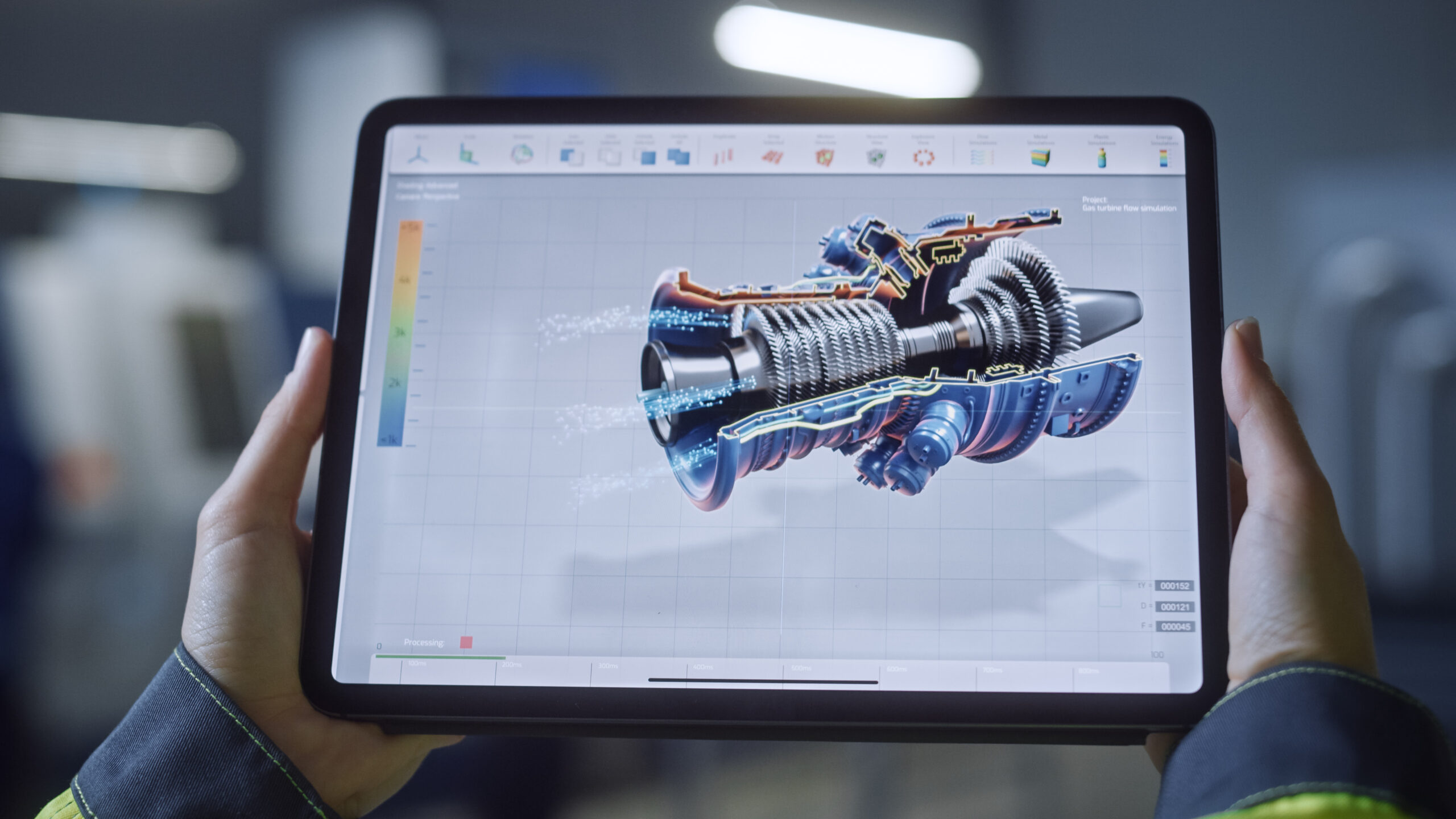
Entreprendre une démarche d’amélioration continue au sein d’une entreprise, c’est s’assurer au quotidien de gagner en performance globale et industrielle et atteindre ainsi ses objectifs. Il existe désormais une vaste gamme d’outils et de méthodes au service des entreprises permettant de mettre en place leur processus d’amélioration continue.
Qu’est-ce que l’amélioration continue ? Quels sont les outils permettant de mener à bien cette démarche ? Nos experts ARVEESIO répondent à vos questions dans cet article.
Qu’est-ce qu’une démarche d’amélioration continue ?
La démarche d’amélioration continue repose sur un vaste champ d’actions durables mis en œuvre dans le but d’améliorer l’ensemble des processus d’une entreprise.
Elle est basée sur deux principes fondamentaux notamment :
- L’élimination des dysfonctionnements ;
- Le renforcement des atouts générateurs de valeur.
Ces principes permettent de réévaluer de façon régulière, les procédés utilisés, de les remettre en question afin de favoriser une croissance durable de l’entreprise.
Entreprendre une démarche d’amélioration continue au sein d’une entreprise va permettre de :
- Booster progressivement la croissance ainsi que le rendement global de l’organisation ;
- Réduire les coûts ;
- Améliorer l’efficacité, la productivité et la rentabilité de la société.
Quels sont les principaux outils et méthodes d’amélioration continue ?
Plusieurs méthodes et outils peuvent être utilisés pour piloter votre démarche d’amélioration continue. Ces systèmes de management sont adaptés à toutes les situations comme par exemple, évaluer un scénario précis, identifier des sources de gaspillage ou encore piloter un plan d’action.
Découvrez ci-dessous quelques outils d’amélioration continue.
Le Lean Management pour éliminer les sources de gaspillage
Le lean management est une méthode inspirée par le système de production de Toyota. Cette méthode souhaite améliorer les performances de l’entreprise, ainsi que sa rentabilité.
Elle est basée sur les actions ci-après :
- Supprimer chaque source de gaspillage (tâches superflues, opérations inutiles, compétences inexploitées, éléments non créateurs de valeur, temps de latence, surproduction, mauvaise gestion des stocks…) ;
- Optimiser tous les process de l’entreprise.
Roue de Deming ou PDCA pour une amélioration continue
La roue de Deming ou PDCA est une technique d’amélioration continue qui présente quatre étapes à suivre de façon répétitive. Ces étapes ont pour objectif d’améliorer un fonctionnement déjà existant (procédés, organisation, produit, etc.).
Les quatre phases à suivre successivement sont :
- Prévoir (Plan) : cette première étape vise l’analyse de la problématique rencontrée ainsi que les moyens disponibles. Elle comporte également l’élaboration d’un plan d’action approprié, sur la base d’indicateurs clés, afin d’évaluer en aval, l’impact des résultats ;
- Faire (Do) : cette étape correspond à la mise en place d’un plan d’action concret auprès de l’ensemble des acteurs concernés ;
- Vérifier (Check) : la vérification consiste à l’évaluation des résultats grâce aux indicateurs de performance. En fonction des résultats, le responsable doit émettre et appliquer les solutions correctives ;
- Réagir (Act) : cette étape correspond au bilan de fin de cycle. Si le but n’est pas atteint les dirigeants peuvent procéder au déploiement d’un nouveau cycle.
La Roue de Deming, aussi appelée Cycle PDCA, est l’élément central sur lequel repose une démarche d’amélioration continue.
La démarche Kaizen pour une amélioration quotidienne
Le mot »Kaizen » est un mot japonais qui signifie en français »changement vers le meilleur ». La méthode kaizen est également une méthode d’amélioration continue.
Elle recommande une transformation globale des process de l’entreprise, au moyen de petites modifications régulières et progressives implémentées quotidiennement.
Cela peut par exemple passer par :
- Un changement d’une partie ou d’un changement global de la culture d’entreprise ;
- L’analyse quotidienne des objectifs et des performances ;
- La conception d’un planning de motivation du personnel ;
- La mise en place d’un système de travail de groupe ;
- Etc.
Ce changement suggère nécessairement un engagement total de la part de l’ensemble des partenaires.
Le système Kaizen se sert lui-même d’autres outils de l’amélioration continue tels que :
- Le lean management ;
- La roue de Deming ;
- Le TQM (Total Quality Management) ;
- La méthode 5S.
La méthode des 6 Sigma pour une amélioration de la production
La méthode des 6 Sigma quant à elle, vise la production d’une qualité optimale des produits et services. Elle regorge des techniques qui visent l’amélioration des processus de production de l’entreprise. Elle est mise en place grâce au recueil des avis des clients d’une part(enquêtes, questionnaires de satisfaction, etc.)et à des indicateurs pertinents d’autre part.
La démarche des 6 Sigma est basée sur la méthode DMAIC. Elle s’articule autour de cinq étapes, notamment :
- Define : définition de l’objectif à atteindre ;
- Measure : évaluation des attentes des clients ;
- Analyse : analyse des problèmes rencontrés, identification des forces et des faiblesses ;
- Improve : mise en place des solutions correctives et innovantes afin d’améliorer les process ;
- Control : maintenance du niveau de qualité sur la durée.
Les 7S de McKinsey pour une vue d’ensemble
La méthode de McKinsey est un outil qui a vu le jour dans les années 80. Il permet d’évaluer les performances internes de l’entreprise sur la base des 7 variables ci-après :
- Strategy : orientations stratégiques et procédés mis en place pour les atteindre ;
- Structure : structure organisationnelle de l’entreprise (organigramme, liens, délégation, hiérarchie, répartition des tâches…) ;
- Systems : modes de fonctionnement, procédures, et méthodes utilisées au sein de l’entreprise ;
- Style of management : le style de management mis en place (délégatif, participatif, autoritaire, etc.) ;
- Skills : les compétences qui renforce toute la valeur ajoutée de l’entreprise (compétences, expérience, organisation, expertise…) ;
- Staff : l’aspect social, la gestion des ressources humaines (motivation, épanouissement des salariés…) ;
- Shared values : la culture et les valeurs partagées au sein de l’entreprise.
Grâce à l’analyse de ces six aspects au sein de l’entreprise, il est plus aisé d’avoir une vue d’ensemble de l’organisation ; et de procéder à un état des lieux exhaustif. Cet état des lieux va permettre d’adapter la démarche d’amélioration continue en fonction de ses résultats.
Les 5 S pour optimiser l’environnement de travail
Méthode de management d’origine japonaise conçue par Toyota, a été initialement conçue pour améliorer les conditions de travail au sein des ateliers de production. Aujourd’hui, cette méthode peut être appliquée dans tous les secteurs d’activités. Elle se résume en 5 étapes, à réaliser de façon consécutive :
- Seiri : se débarrasser de tout ce qui n’est plus utile ;
- Seiton : organiser minutieusement tout ce qui est utilisé au quotidien dans un espace approprié ;
- Seiso : toujours garder les outils ainsi que l’espace de travail propre, sain et sécurisé ;
- Seiketsu : maintenir de façon permanente, la propreté des lieux et le rangement des outils ;
- Shitsuke : être très rigoureux et respecter l’ordre chronologique de chaque étape précédentes l’une après l’autre.
Vous souhaitez optimiser la performance industrielle de votre entreprise ? Vous visez l’amélioration des processus internes ? Grâce à notre solution de maintenance industrielle assistée par réalité augmentée, bénéficiez de gains de temps et d’argent considérables. Contactez-nous et notre équipe s’occupera de vous dans l’immédiat !